At the 2014 Sea Air Space Show in Maryland, April 7 – 9, United Electronic Industries (UEI) will demonstrate the newly released DNR-MIL and DNA-Mil Data Acquisition and Embedded Control Chassis. These Mil-Grade platforms are ruggedized, performance optimized, designed to meet key elements of MIL-STD-461/810/1275 and guaranteed to withstand 5 g vibration and 100 g shock for the most environmentally challenging I/O applications.
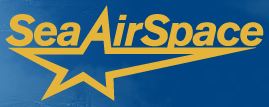
The 2014 Sea Air Space Exposition will be held on April 7-9 at the Gaylord National Convention Center in National Harbor, MD.
Configurable as either a stand-alone or computer-hosted system, these I/O test and embedded control instruments are 100% COTS solutions, meaning they are modular and customizable for handling any analog, digital, interface, sensor/transducer input or output. Their rugged IP66/NEMA6 sealed chassis allow for in-field deployments without any additional enclosure or protection required.
For long-life I/O systems like Line Replaceable Units (LRUs) and VME-based systems that will soon face end-of-life availability issues, UEI guarantees at least 10 years of post-purchase product availability. Extensive software support includes all popular OS, RTOS and DAQ (data acquisition) applications, including Linux, VxWorks, Windows, MATLAB, Simulink, QNX and RTX to name a few.
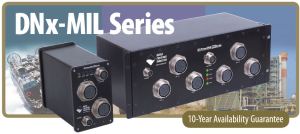
The new DNA-MIL and
DNR-MIL platforms are designed for MIL-STD-461/810/1275
compliance and for environmentally harsh I/O acquisition and control applications.
Much like it’s predecessor systems, the DNX-MIL products are made in the USA and supported by UEI’s extensive line of of analog, digital and interface I/O boards for thermocouples, RTDs, ICP/IEPE, ARINC-429, AFDX, MIL-STD-1553, CANbus, RVDT/LVDT, synchro/resolver, RS 232/422/485 strain gauge, quadrature encoder, high-voltage analog outputs, high drive current, analog inputs up to 24-bits, arbitrary waveform generation and much more.
For the most robust I/O connectivity with on-board Built-In-Test (BIT) diagnostics to ensure maximum uptime and failsafe operation, the DNx-MIL Chassis can’t be beat. Give us a call for more details.